The Internet of Things (IoT) permeates everyday life around the globe. From smart TVs to appliances, the IoT gives organizations an opportunity to learn more about consumers’ spending habits, behaviors and more.
Adoption of IoT devices is particularly beneficial to manufacturing and supply chain operations that manage a large number of assets and complex distribution processes. The IoT promises to boost productivity, productivity and profitability by improving decision-making and redefining how people and machines interact with each other.
However, the IoT goes beyond the private sector; it has wide-ranging implications and benefits for military logistics and supply chain management. Connected devices in the military promise to revolutionize modern warfare by leveraging automation, Big Data and analytics. This will provide greater lethality and survivability for our warfighters, while reducing cost and increasing efficiency.
“IoT devices can gather more data, facilitate more complex analysis and faster reactions, and reduce human error, delivering more precise and efficient military capabilities, according to a CSIS report, “Leveraging the Internet for a More Efficient and Effective Military.”
Challenges in Adopting IoT for Military Applications
The DoD continues to drive innovation in advanced sensors and control systems, “but it is falling behind in deployment of IoT technologies that have the potential to deliver new capabilities and cost savings,” according to CSIS authors Denise E. Zheng and William A. Carter.
Like commercial operations, the DoD continues to struggle with interoperability. While the military has deployed a wide range of IoT-related technologies, many are developed in segregated “stovepipes” which makes it difficult to communicate across other systems.
The DoD has also connected millions of sensors through extensive network infrastructures, but few leverage the full capabilities of the IoT – namely connected sensors, automation and digital analytics.
Enterprise Sensor Integration: The Gateway to the IoT
Tapestry Solutions, a leader in information management software and services, has addressed these challenges with its Enterprise Sensor Integration (ESI) solution. ESI is a revolutionary integration platform that provides a centralized hub for any sensor, regardless of hardware type or brands.
The technology automates workflow processes and integrates digital analytics, enabling commanders and logisticians to easily digest massive amounts of data to facilitate relevant, instant decision-making. ESI significantly optimizes asset tracking, inventory management, warehouse and fulfillment operations, and workflow management.
To truly understand why ESI is key to leveraging the IoT in defense supply chains of today, however, let’s take a look at defense supply chains of the past.
A Flashback to the Gulf Wars
For decades, the U.S. military has faced a widespread problem: a lack of visibility into supply and demand. When a soldier needed something, uncertainty surrounded the order.
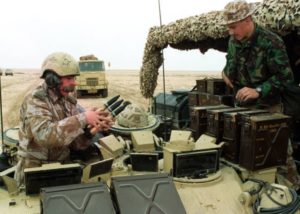
Photo: David Giles / Getty Images
Questions undoubtedly arose: Where’s my stuff? When will it get here? How long will it be before another shipment arrives? How much do I have right now?
During Operation Storm, for instance, these questions led to frequent instances of over-ordering supplies – or “just-in-case” stockage – a standard practice in all ranks in the military. However, this practice of hoarding backfired. The units that depended on just-in-case stockage experienced extended wait times until they receive needed parts.
During Desert Storm, the just-in-case logistics system was so severely hindered by misprioritized shipments that high-priority items, such as food, ammunition, and fuel, were not delivered to participating units in a timely manner. To avert the possibility that units might run out of critical supplies, a ‘work-around’ just-in-time distribution system called Desert Express was developed,” according to Army Logistician.
After the war ended, assets ranging from package-level supplies to artillery and armored vehicles were left in the field or warehouses for use by allied forces in Iraq, aid workers and contractors.
As military conflict returned to the region in the second Gulf War, U.S. soldiers were taking advantage and using the resources left behind from the First Gulf War. Unfortunately, much of the weapons and equipment left behind had grown old with advances in battlefield technology. The use of these left-behind assets led to even more significant confusion as the military realized millions of dollars were lost.
Poor Accountability = Losses and Risk
The problem continued during the second Gulf War with the massive withdraw of U.S. troops from Iraq in 2011. Rather than ship everything home, the U.S. handed over military bases and millions of pieces of equipment – worth billions to the Iraqi government, according to the Huffington Post.
In September 2011, the Government Accountability Office (GAO) issued a report, GAO-11-774 noting that after one of the largest base transitions to date, “officials said they were surprised at the amount of unaccounted-for equipment that was left over at the end of the transition process.”
In one year alone, over 2.4 million pieces of equipment worth a total of $250 million had been given away to the Iraqi government, including tanks and trucks to office furniture and latrines. Unfortunately, many items were unaccounted for.
Some assets could have simply piled up in Iraq since combat operations began in 2003 and were not properly logged, according to the report. The GAO warned that “units sometimes turn in such equipment without paperwork and have even removed identifying markings such as serial numbers to avoid retribution.”
Better tracking of assets was the end-all solution presented in the GAO report, but it had a more profound reason than just cost-savings. It could prevent equipment, weapons and uniforms from falling into the enemies’ hands.
The problem continued in 2013 with missing assets in Afghanistan. The DoD Inspector General published a summary of an audit report revealing that the U.S. military “did not report in a timely manner 15,600 pieces of missing equipment valued at approximately $419.5 million,” according to ABC Denver. In the report, Army officials were criticized for poor accounting and oversight.
Technology Used for Tracking Continued to Lag, Reducing Visibility
Radio frequency identification (RFID) tags were available at this point and widely used in the private sector, such as retail outlets like Walmart. RFID also had promising applications for military asset tracking and supply chain visibility, but investing in them was counterproductive.
The costs of tracking package-level items with active RFID (aRFID) or passive RFID (pRFID) was significant; thus, the military relied mostly on barcoding.
Barcodes were placed on all assets and supplies, ranging from aircrafts to item-level packages. While effective at tracking items, this process lacked real-time applicability. Information scanned was only as good as its last time of scanning.
Barcodes were also slow and cumbersome. The technology required direct line of sight and lacked accuracy, according to Mojix. The lack of asset visibility, in turn, resulted in the continued practice of over-ordering and unaccounted-for assets.
Automation: The Key to Total Asset Visibility, Improved Productivity and Cost-Savings
The problem was compounded because data collection was dependent on manual entry. The lack of automation – along with a fragmented information technology (IT) structure and limited processing of data – contributed to further inaccuracies in data collection, storage, retrieval and analysis.
When the U.S. turned over forward-operating bases to local forces in the Middle East, for example, the military could not determine the actual value or location of all assets and equipment left behind. Due to manual data entry, information and accountability got lost amid the paperwork.
The natural solution to this problem is automation; however, automation depends on solid IT structure. The best-laid plans for system data collection and automation will fall short if a network cannot realistically communicate with individual sensors and interfaces. All components of an IT network must function as one to provide a clear, crisp image of overall supply chain asset location, movements and planned deployments or shipments.
Moving from manual entry and application to automation leads to better analyses and review of data to enhance supply chain accountability and visibility. Furthermore, leveraging Big Data and analytics through an IoT-based platform like Tapestry’s ESI solution, can help commanders achieve a 360-degree view of all military assets, regardless of time or location.
On the battlefield, this translates into fewer instances of lost, unaccounted-for equipment and lowers the risk of expensive, if not dangerous, military equipment falling into the wrong hands.
What’s Next?
Military logistics networks face an uphill battle when using outdated, manual processes to track and manage supply chain assets. Rather than leaving many supplies, assets and resources in potentially hostile territories upon withdrawal from times of war, military forces need a way to gain accurate, real-time visibility and accountability into their logistics’ networks.
ESI addresses these challenges with its sensor-agnostic IoT platform that enables various sensor technologies and networks to talk with one another. But how exactly does implementing IoT technologies via ESI lead to better asset tracking for defense organizations? How does integration of IoT technologies prevent the recurrence of the disastrous state of DoD logistics that arose during the Gulf Wars?
Stay tuned. We answer those questions in the next blog of this two-part series.
The appearance of U.S. Department of Defense (DoD) visual information
does not imply or constitute DoD endorsement.
Contact:
Janet Dayton
Tapestry Solutions Inc.
tapestrymarketing@boeing.com