BAE Systems has been recognized for its smart factory transformation using radio-frequency identification (RFID) technology to track and manage assets/tools, inventory and workflow processes. The company captured an award for the Best Manufacturing RFID Implementation at the 17th annual RFID Journal LIVE conference after demonstrating significant savings using RFID-enabled technology developed by Tapestry Solutions, a division of Boeing Global Services.
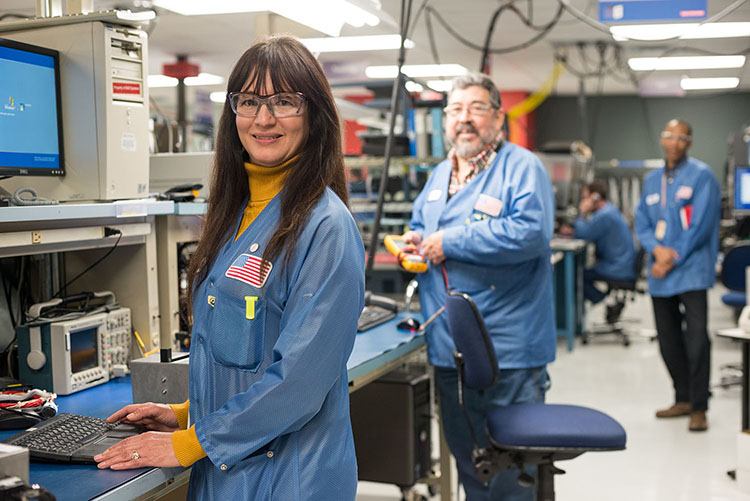
BAE Systems’ team members, pictured during production.
BAE Systems leveraged Tapestry’s Enterprise Sensor Integration (ESI) technology to connect RFID-tagged materials with its enterprise resource planning systems – setting the stage for an Industrial Internet of Things (IIoT) ecosystem. Within the first year of deployment, BAE Systems reported that it saved 2,400 hours tracking work-in-progress, or WIP, and saved 1,248 hours in searching for missing items. The solution has also significantly accelerated manufacturing processes while improving quality.
“The BAE Systems’ program was an excellent example of how RFID and the right software can drive real value for companies. It was truly an award-winning project that demonstrated how RFID can translate into quantifiable results for a major enterprise,” said Mark Roberti, founder and editor of RFID Journal.
The conference is the world’s largest RFID venue, with several domestic and international companies vying for the Best Manufacturing RFID Implementation award. The winners were selected from six different end-user categories.
A highlight at the conference was the keynote address delivered by Deirdre (Dee) Schmidt, BAE Systems’ Operational Excellence Leader, who spearheaded the RFID initiative at the Electronic Warfare Integrated Manufacturing Center (EW-IMC) facility and several other plants. She described the program’s three-pronged objective of automating inventory replenishment, managing the status and location of asset and tools, and improving visibility of WIP.
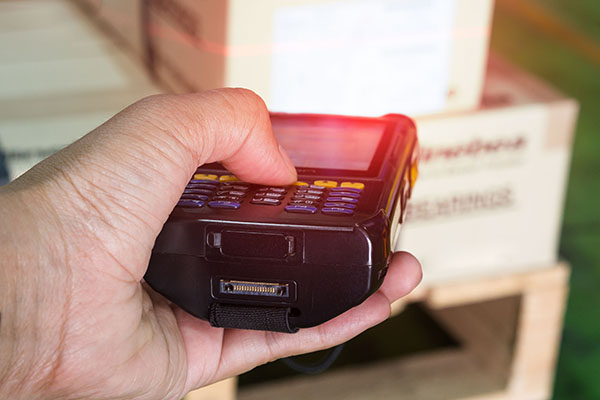
RFID barcode scanners track the location and condition of tagged assets at BAE Systems.
Prior to the RFID-enabled system, BAE Systems had a largely manual process for tracking and managing supply inventory, assets and tools, as well as workflow on the assembly floor. The firm used a time-intensive barcode scanning process to track and replenish inventory at multiple sites. Procurement teams also released orders manually, which often resulted in longer than desired lead times.
To address these challenges, Tapestry provided the ESI/RFID solution in 2017, leveraging the same sensor fusion technology that it implemented across 27 major Boeing manufacturing sites incorporating over 300 buildings. The ESI solution saved Boeing $100 million in its first year alone, and today processes 6 to 10 billion tags each week.
At BAE Systems, the RFID/ESI solution is currently tracking over 200,000 assets, 30,000 parts and an estimated 6,500 work orders at its facilities. The automation of material replenishment has enabled BAE Systems to transform from a “push” scheduling process to a “pull,” where there is a just-in-time inventory flow through its supply chain. The tool and asset tracking solution enables users to identify items as they enter and return from specific zones with associated alerts. It also monitors recalibration due dates on specific equipment.
ABOUT ESI
ESI is a middleware software solution that connects people, processes and data to improve visibility in the factory – and across an entire enterprise. ESI solves interoperability challenges due to the growing number of disparate tracking technologies that speak different languages.
ESI integrates a myriad of sensor technologies that track, monitor and control assets and workflow processes – providing the gateway to the Internet of Things and smart factory transformation. As a “sensor-agnostic” solution, ESI can be integrated with an organization’s legacy RFID and sensor systems, regardless of hardware or sensor types or brands.