BAE Systems has been recognized for its smart factory transformation using radio-frequency identification (RFID) technology to track and manage assets/tools, inventory and workflow processes. The company captured an award for the Best Manufacturing RFID Implementation at the 17th annual RFID Journal LIVE conference after demonstrating significant savings using RFID-enabled technology developed by Tapestry Solutions, a division of Boeing Global Services.
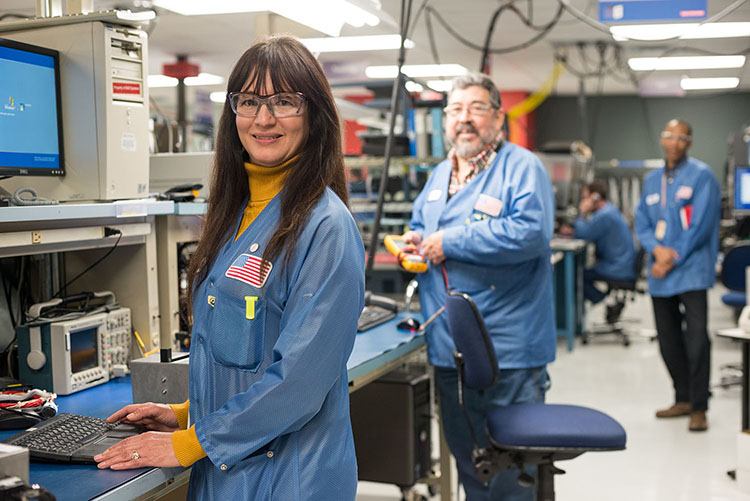
BAE Systems’ team members, pictured during production.
BAE Systems leveraged Tapestry’s Enterprise Sensor Integration (ESI) technology to connect RFID-tagged materials with its enterprise resource planning systems – setting the stage for an Industrial Internet of Things (IIoT) ecosystem. Within the first year of deployment, BAE Systems reported that it saved 2,400 hours tracking work-in-progress, or WIP, and saved 1,248 hours in searching for missing items. The solution has also significantly accelerated manufacturing processes while improving quality.
“The BAE Systems’ program was an excellent example of how RFID and the right software can drive real value for companies. It was truly an award-winning project that demonstrated how RFID can translate into quantifiable results for a major enterprise,” said Mark Roberti, founder and editor of RFID Journal.
The conference is the world’s largest RFID venue, with several domestic and international companies vying for the Best Manufacturing RFID Implementation award. The winners were selected from six different end-user categories.
A highlight at the conference was the keynote address delivered by Deirdre (Dee) Schmidt, BAE Systems’ Operational Excellence Leader, who spearheaded the RFID initiative at the Electronic Warfare Integrated Manufacturing Center (EW-IMC) facility and several other plants. She described the program’s three-pronged objective of automating inventory replenishment, managing the status and location of asset and tools, and improving visibility of WIP.
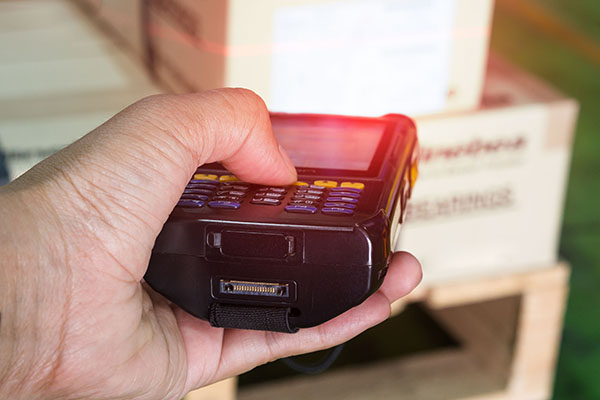
RFID barcode scanners track the location and condition of tagged assets at BAE Systems.
Prior to the RFID-enabled system, BAE Systems had a largely manual process for tracking and managing supply inventory, assets and tools, as well as workflow on the assembly floor. The firm used a time-intensive barcode scanning process to track and replenish inventory at multiple sites. Procurement teams also released orders manually, which often resulted in longer than desired lead times.
To address these challenges, Tapestry provided the ESI/RFID solution in 2017, leveraging the same sensor fusion technology that it implemented across 27 major Boeing manufacturing sites incorporating over 300 buildings. The ESI solution saved Boeing $100 million in its first year alone, and today processes 6 to 10 billion tags each week.
At BAE Systems, the RFID/ESI solution is currently tracking over 200,000 assets, 30,000 parts and an estimated 6,500 work orders at its facilities. The automation of material replenishment has enabled BAE Systems to transform from a “push” scheduling process to a “pull,” where there is a just-in-time inventory flow through its supply chain. The tool and asset tracking solution enables users to identify items as they enter and return from specific zones with associated alerts. It also monitors recalibration due dates on specific equipment.
ABOUT ESI
ESI is a middleware software solution that connects people, processes and data to improve visibility in the factory – and across an entire enterprise. ESI solves interoperability challenges due to the growing number of disparate tracking technologies that speak different languages.
ESI integrates a myriad of sensor technologies that track, monitor and control assets and workflow processes – providing the gateway to the Internet of Things and smart factory transformation. As a “sensor-agnostic” solution, ESI can be integrated with an organization’s legacy RFID and sensor systems, regardless of hardware or sensor types or brands.
Contact:
Janet Dayton
Boeing Global Services
janet.l.dayton@boeing.com
Moving from Hype to Reality in the Application of the Industrial Internet of Things, or IIoT, for Manufacturing Operations
Tapestry Solutions has pioneered the use of the Industrial Internet of Things (IIoT) for manufacturing operations – turning hype into reality when it rolled out its Enterprise Sensor Integration (ESI) platform across 50 Boeing factories.
For this monumental achievement, The Internet of Things Institute, Inc. has included Tapestry’s IoT technologies in its listing of the Top 20 Industrial IoT Applications. The Top 20 list includes companies that are “not idly boasting about the promise of the IIoT to transform their business; they have already begun the transformation,” according to the Institute.
As noted in the listing for Boeing: Using IoT to drive manufacturing efficiency:
“Aviation pioneer William Boeing quipped that it “behooves no one to dismiss any novel idea with the statement, ‘It can’t be done.’”
The multinational aviation company founded in Boeing’s name apparently still subscribes to that ethos … Boeing and its Tapestry Solutions subsidiary have aggressively deployed IoT technology to drive efficiency throughout factories and supply chains…”
As a sign of aggressive deployment of its IIoT application, Tapestry recently completed the initial phases of an ESI installation for a major defense contractor. The technology will provide the customer with automated asset tracking, workflow and material replenishment processes at their assembly plants throughout the United States.
About ESI
Tapestry’s ESI is an innovative integration platform that connects disparate sensor technologies through a standard interface – seamlessly connecting people, data and processes through automation. The technology addresses concerns surrounding interoperability between devices and machines that use different protocols with different architectures.
With ESI, there’s just one platform that can communicate with many different hardware and software vendors’ IoT solutions. As a result, supply chain visibility is not completely dependent on one manufacturer or sensor type. This ensures total asset visibility of equipment, tools, cargo and processes anywhere in the world.
The sensor integration solution saved Boeing over $100 million in its first year alone. It continues to generate savings year after year due to improved productivity, reduced inventory costs and increased supply chain velocity.
Unlike other IoT sensor solutions, ESI is a cloud-based platform that can be implemented across a global enterprise. In addition to manufacturing applications, ESI supports global supply chain logistics for industries including pharmaceutical, automotive, aerospace and defense.
Contact:
Janet Dayton
Tapestry Solutions Inc.
tapestrymarketing@boeing.com
Tapestry to Integrate its IoT Platform for Major Defense Manufacturer
Tapestry Solutions has entered into another agreement with a major defense manufacturer to integrate Tapestry’s Enterprise Sensor Integration (ESI) software at its assembly plants throughout the United States. The technology will provide the defense contractor with automated asset tracking, workflow and material replenishment processes using touchscreen monitors and handheld RFID readers.
The first installation is set to go live in August, with additional installations expected to follow at more than two dozen plants under a multi-phase project approach.
“We are proud to offer a package that no other vendor was able to match,” said Michael Spencer, Vice President of Global Sales and Marketing, Tapestry Solutions. “The customer made it clear that they chose Tapestry because no other vendor demonstrated our unique understanding of the Internet of Things (IoT) hardware, software, operations and customer centric implementation.”
Unlike other sensor solutions, ESI is a sensor-agnostic IoT platform that can be scaled across the global enterprise. It is also available as a cloud-based solution for factories of all sizes and supply chain operations.
With ESI, supply chain visibility is not dependent on one manufacturer or sensor type. ESI interfaces with major RFID vendors as well as sensor solutions from providers including Oracle, SAP and IBM Maximo. This ensures total asset visibility of equipment, tools, shipments and processes anywhere in the world.
ESI is based on automated information technology that Tapestry rolled out across 50 Boeing plants. Boeing reported a savings of more than $100 million during its first year by reducing labor costs, increasing workflow efficiency, preventing asset theft, lowering rental equipment expenses and improving decision making based on the analytic data. Tapestry estimates a recurring savings for Boeing of $70 million annually.
As a result of the successful implementation at Boeing, Tapestry launched the commercially available ESI product line in November 2016.
Media Contact:
Janet Dayton
tapestrymarketing@boeing.com
Tapestry Solutions Launches IoT Sensor Integration Solution; ESI Leverages Enterprise Technology Deployed at Boeing
SAN DIEGO, November 16, 2016 – Tapestry Solutions, Inc., a non-fully integrated subsidiary of Boeing [NSYE: BA], has launched its Enterprise Sensor Integration (ESI) software platform that will transform supply chain operations and help businesses tap the power of the Internet of Things (IoT). Tapestry’s ESI middleware solution seamlessly connects people, processes and data on factory floors, supply chains, and across the enterprise. By providing a standard infrastructure for data and analytics, ESI gives decision-makers a complete picture of their inventory and asset movements during the production process.
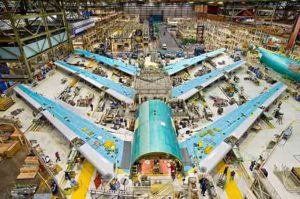
Wing Sets in the 747 Factory in Everett
(Photo: Jeff McNeil/Wikimedia Commons)
“ESI is a game-changer in the industry. It will modernize supply chain and manufacturing operations, and in the process, help businesses grow their bottom line,” said Robin Wright, President & CEO of Tapestry Solutions, Inc.
ESI is based on Tapestry’s field-proven technology recently deployed at 50 sites throughout The Boeing Company – the world’s largest aerospace company. At Boeing, the custom technology is known as the Automated Identification Technology – Information Management System, or AIT-IMS. In its first year alone, AIT-IMS saved Boeing approximately $100 million through decreased assembly time, automated asset receipt/payment, enhanced inventory management and improved quality and safety.
The software harnesses the power of Big Data, boosting manufacturing efficiency, productivity and profitability. It serves as the foundation for the IoT, where internet-enabled devices are connected, intelligent and interactive.
“ESI not only will give businesses a competitive advantage, it will also help accelerate industry innovation around the globe. We are proud to be part of this IoT sensor revolution,” added Jens Pohl, Vice President of Engineering, Tapestry Solutions.
Tapestry’s commercially available ESI solution features expanded capabilities, including a cloud-based platform and integration with temperature sensors, thermostats, pressure sensors and humidity sensors.
Through data fusion, ESI integrates a myriad of sensor technologies that track, monitor and control assets and workflow processes on a common platform. It synthesizes data from sensors, software and electronics – everything from bar codes, active and passive RFID, Wi-Fi and GPS tags to scanners and ultra-wideband wireless systems can securely and seamlessly interact with one another.
ESI also unlocks the massive opportunity of the future IoT, where everything is smart and interconnected – from smart cities and homes to smart factories. From a manufacturing perspective, the sensor management system is not limited to tracking assets and enhancing supply chain visibility, however. It can also be linked to a building’s infrastructure and equipment, such as managing and controlling heating, lighting and door security systems as well as machine sensors.
The enterprise-class platform has interconnected nearly every aspect of Boeing’s asset management and supply chain. As a result of its successful implementation, AIT-IMS will serve as the platform for Boeing’s IoT integration efforts. (See AIT-IMS Case Study)
Tapestry Solutions, Inc. is a global provider of information management software and services for defense, government and commercial markets. Backed by our parent company, The Boeing Company, we help solve logistics challenges for the world’s largest and most complex supply chains. We also provide mission planning, training and simulation support to maximize readiness for our warfighters. Headquartered in San Diego, Calif., Tapestry supports customers from more than 50 locations around the world, including Saudi Arabia, Oman, Afghanistan, Kuwait, the UK, South Korea, Australia and Germany.
Media Contact:
Janet Dayton
tapestrymarketing@boeing.com